Analysing Data Beyond Your Incident Management System – Maritime Safety
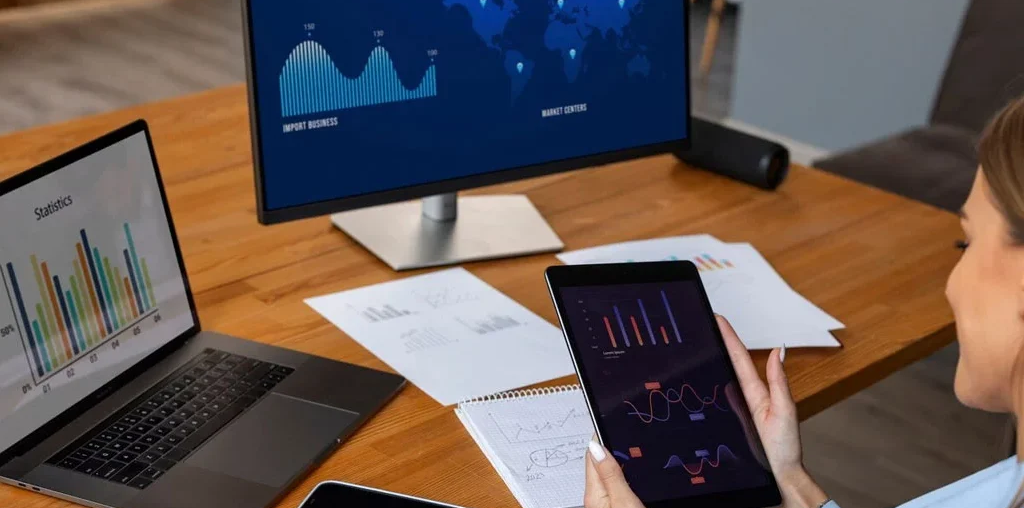
Traditionally, shipping companies have relied purely on the data from their incident management systems (IMS) to help them discover and fix onboard issues.
This data is useful, but incomplete. An IMS will usually only show the specific reason for an incident occurring, rather than including all the underlying issues that lead up to that point. In other words, while you may be able to fix an individual incident, you are not solving the root of the problem and it may occur again in the same way.
Hilo can help you improve your maritime safety by using a fully comprehensive dataset: the key aspect to producing useful fleet risk management data analysis. The starting point is the data you have, but don’t use to its full potential.
Look Beyond Your IMS
The first thing is to look beyond the traditional data source—your IMS. There are 2 other significant types of data available:
- Vetting/audit data
- Defect/maintenance data
Within these three data sources, there are over 500 different datasets available, including defect logs, maintenance logs record books entries, internal audit reports, external audit reports, SIRE inspections, PSC inspections, owner/charterer inspection reports and Class surveys.
These all contain valuable information – but it takes time and effort to compile and standardise the data for effective analysis. The importance of merging, consolidating, and standardizing such data cannot be overemphasised. Data must be structured to be analysed properly.
But this takes time. That is why the majority of shipping companies do not currently use this data. It is not because it would not be useful. It is simply a question of practicality.
Successful fleet risk management analysis
It is clear that in order to improve your maritime safety for the long term, you need to understand the full picture of safety in your fleet. Any analysis you undertake with incomplete data will be inherently flawed, because you are missing vital information.
But there are 3 questions:
- What is the value of looking outside the Incident Management System?
- What data do you need to make your fleet risk management analysis effective?
- And, most of all, how can companies find the time and resources for analysing data?
Ensure the best ship risk prediction
Inspection and maintenance data both capture small but useful leading indicators which may have a sizeable impact on the safe operation of a vessel and its equipment.
By using all your vetting and inspection data, you can gain a clear indication of anything out of the ordinary. These may be minor at the time of inspection, but if not attended to could turn into an uncontrollable risk within your fleet.
As an example, firstly consider a vessel that has never had a steering gear failure – and therefore no data relating to this in its IMS – but which has suffered multiple leakages to its steering gear system the past few months.
The leaks, as a leading indicator revealed by maintenance reports, could subsequently be the cause of a major but foreseeable equipment failure. It is critical that these issues are spotted and fixed rapidly, before it is too late to avoid a catastrophe.
Now examine the same situation, but from the viewpoint of an internal audit. During the steering drills prior to approaching a sensitive and congested port, it was found that the bridge and engine watchkeeper were not familiar with emergency steering gear procedures and were not equipped to take actions in case of a main steering gear failure and avoid collision while manoeuvring. By fleet risk management analysis of audit data, HiLo can identify where gaps need to be filled, preventing small incidents from developing into large-scale disasters.
By using IMS data alone, you cannot anticipate and stop maritime disasters. But by using all available data, you can.
Avoid problems reoccurring
As for the second question, what data should you use? A simple answer – everything available. The more facts used to derive a fleet risk management analysis, the more thorough and accurate it will be.
The greatest advantage of this is that by using all the available data, and performing the best analysis, you not only fix current issues, but stop them reoccurring. You can even anticipate future problems before they occur, stopping minor issues that could develop into major catastrophes.
Finding the time
So you know what data to use, and why. Now the biggest problem – how do you mine it and how do you utilise it profitably, with so much time pressure?
The problem is that with so much mandatory safety work and paperwork already to do just to satisfy legal requirements, your crew and shore teams simply cannot take on extra, ‘voluntary’ paperwork – no matter how useful.
It is a deeply frustrating situation – but fortunately HiLo can help.
HiLo developed Pinpoint, our world-leading maritime decision-support system. Pinpoint can process and analyse a wide variety of data. This include sorting and standardising raw data, across many different formats, so uploading the information is a quick process. Just drag and drop your files into our portal. This eliminates the issue of not being able to use or cleanse data. Pinpoint does everything for you, for all data collection.
Pinpoint is your very own digital HSE manager. It analyses hundreds of thousands of data points from the 3,500+ vessels in the HiLo fleet, and brings them all together to give you insights that can’t be found anywhere else in the industry.
But most shipping companies do not have the resources for analysing data, spotting trends, drawing conclusions and finding tailored solutions for their own vessels.
Your tailored maritime safety strategy
The value is clear. The data is available. But the time for analysis is not. How do we solve this final dilemma, and put that data to use in saving lives?
Fortunately, HiLo can also help here. Our personalised maritime safety strategy for companies, MISS, takes away the effort of translating our analysis into tangible actions. Based on your data and your unique risks, it acts like an extra team member so you can improve safety with minimal resources. And no ordinary team member, but one that has experience on thousands of ships, and has learned from hundreds of incidents.
MISS gives you a structured action plan based on the needs of your fleet. We prioritise the risks which will have the biggest impact on crew safety, and explain exactly how to solve each one through a simple step-by-step process.
So how do you find the time? You don’t have to – we do everything for you.
Data beyond your IMS is valuable. It always has been. But companies have lacked the time and personnel to use this information to save money, time and lives at sea. Now you can. And with HiLo you will – the results of HiLo’s customers speak for themselves.
From 2020-2021, Tankers in our fleet have experienced:
- 308 fewer high-impact / potential high-impact events
- 19 fewer major spills
- 9 fewer serious injuries
Bulk carriers working with us have seen:
- 135 fewer high-impact / potential high-impact events
- 24 fewer serious injuries
The full HiLo fleet, including OSVs, container ships and near coastal tankers, has seen:
- A 5% reduction in spills
- An 8% reduction in injuries
- A 12% overall incident reduction.
Each HiLo customer has saved an average of $3 million annually.
Save your seafarers’ time – and their lives
HiLo’s world-leading technology and innovative approach means we analyse the fullest range of data possible to draw life-saving conclusions. Talk to us to see how it could benefit you.
Request a HiLo demo to see the system for yourself.